Procédé Kaldo
Le procédé Kaldo ou procédé Stora-Kaldo est un ancien procédé d'affinage utilisé en sidérurgie pour affiner la fonte brute phosphoreuse. Il s'agit d'un modèle particulier de convertisseur à l'oxygène pur, dans lequel le brassage du métal en fusion est assuré par la rotation de la cornue. Le nom « Kaldo » est un mot-valise, construit à partir du nom de son inventeur, le professeur Bo Kalling, et de l'usine qui, en 1948, a développé et industrialisé le procédé, la Domnarvets Jernverk.
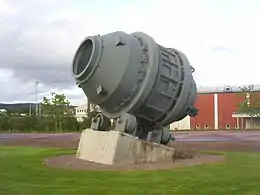
Ce procédé a été adapté à la métallurgie des métaux non ferreux, où il est souvent appelé TBRC (pour Top Blown Rotary Converter). Il y est un outil très polyvalent, autant pour la fusion de déchets riches en métaux précieux que pour l'affinage des mattes de cuivre, de nickel, d'étain ou de plomb.
Histoire
Contexte : mise au point du convertisseur à l'oxygène
Envisagée dès 1856 par Bessemer[1], l'utilisation d'oxygène pur au lieu d'air serait une amélioration logique des convertisseurs Bessemer et Thomas. En effet :
- 78 % de l'air est composé d'azote qui n'a aucun rôle utile dans l'affinage. Injecter ce gaz représente une perte thermique, à peine compensée par le bilan exothermique des réactions chimiques : « chaque m3 d'azote sortant du convertisseur emporte sensiblement la chaleur nécessaire à la fusion d'un peu plus d'un kilogramme de ferraille[2] ».
- la faible teneur en oxygène de l'air ralentit les réactions chimiques ; le soufflage dure plus longtemps puisque qu'on ne peut pas augmenter les débits sans risquer un débordement ;
- une partie de l'azote reste dissout dans l'acier liquide. Or l'azote est un élément fragilisant pour le fer alors qu'une bonne ductilité est essentielle pour les constructeurs automobiles qui recherchent des aciers faciles à emboutir[3], avec des teneurs en azote inférieures à 50 ppm, inaccessibles avec le procédé Thomas[4].
En 1895, Carl von Linde réussit la liquéfaction de l'air. Indépendamment de cette démarche, Georges Claude met en service le un procédé industriel de liquéfaction de l'air. Leurs brevets autorisent la production industrielle, et surtout économique, de grandes quantités d'oxygène et d'azote liquide. Des entreprises naissent rapidement (Claude fonde Air liquide, alors que von Linde crée Linde AG et Praxair)[5]. Cet accès à l'élément clé de la décarburation n'échappe pas à Georges Claude qui recommande dès 1910 l'utilisation de l'oxygène pur en sidérurgie.
Mais le remplacement simple de l'air par de l'oxygène pur présente cependant des difficultés considérables. La réaction de l'oxygène pur avec la fonte mène à des températures de 2 500 à 2 700 °C : dans ces conditions, sans refroidissement des tuyères, le fond d'un convertisseur est détruit en quelques heures[6].
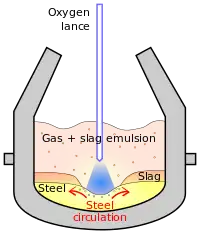
En 1949, Robert Durrer et Theodor Eduard Suess trouvent une solution satisfaisante : ils mettent au point, à l'aciérie VÖEST à Linz, le soufflage d'oxygène au moyen d'une lance pénétrant verticalement dans la cornue. L'invention apparait vite comme une technologie de rupture : six mois après le premier essai, le prototype apparait plus économique que les meilleurs convertisseurs classiques ! Plus efficaces et donc moins nombreux que leurs équivalents à l'air, les nouveaux convertisseurs LD ne demandent qu'un investissement environ deux tiers, et des coûts d'exploitation limités à 55 % de ceux d'une usine classique de capacité comparable[7].
Dans le convertisseur LD, le brassage est assuré par la montée de bulles de monoxyde de carbone issues de la décarburation. Mais ce mouvement, efficace en début de soufflage, tend à ralentir lorsque le carbone dissous passe en dessous de 0,1 %, et le brassage avec le laitier diminue corrélativement. Or l'oxydation du phosphore ne se produit qu'après le départ de tout le carbone, et la capture de l'oxyde P2O5 nécessite un brassage énergique avec la chaux du laitier. L'histoire se répète : comme jadis le convertisseur de Bessemer, le procédé LD révolutionne la sidérurgie mais se révèle inadapté à la déphosphoration[5]. Une variante capable de traiter les fontes phosphoreuses est mise au point : le convertisseur LD-AC, qui consiste à injecter de la chaux en poudre en la mélangeant avec l'oxygène[3]. D'autres déclinaisons sont développées sur ce principe (LBE, LD-Pompey, OLP, etc.), mais le procédé LD perd beaucoup de son intérêt dès qu'on l'emploie à l'affinage des fontes phosphoreuses[5].
Par ailleurs, tous ces procédés mettent en œuvre des réactions chimiques très rapides. Dans les années qui suivent leur apparition, les convertisseurs LD et leurs dérivés sont exclus de l'élaboration d'aciers de qualité[8]. L'apparition de la coulée continue, qui exige un excellent contrôle de la température de l'acier en fusion, nécessite aussi un bon contrôle de l'affinage[9].
Enfin, les convertisseurs à l'oxygène pur génèrent d'énormes quantités de fumées rousses, chargées en oxyde de fer. Le traitement de ces fumées est incontournable. Or les systèmes de dépoussiérage sont coûteux et, même s'ils permettent l'obtention d'un gaz combustible (0,7 GJ/tonne d'acier[5]), avant le premier choc pétrolier, la rentabilité l'investissement est discutable[3].
Développement du convertisseur rotatif
Depuis les années 1940, en Suède, la Domnarvets Jernverk, une usine l'entreprise Stora Kopparbergs Bergslags AB, mène d'actives recherches pour mettre au point un procédé à l'oxygène pur capable de traiter les fontes phosphoreuses. En effet, la fonte brute traitée par l'aciérie de Domnarvet contenant de 1,8 à 2 % de phosphore, l'efficacité de la déphosphoration est un point incontournable[10]. Jusqu'ici, dans un pays où le minerai est bien plus abondant que les ferrailles, le moyen le plus pertinent pour traiter ce type de fonte est le convertisseur Thomas. Mais l'injection d'oxygène dans le convertisseur amène une destruction rapide des réfractaires. Bien qu'en 1940, à Oberhausen, Otto Lellep (1884–1975) parvient à décarburer de la fonte avec de l'oxygène pur, il ne parvient pas à la déphosphorer : avec l'oxygène pur, l'oxydation du phosphore est trop exothermique pour les tuyères du convertisseurs[6].
Pour dépasser 40 % d'oxygène, il faut des diluants plus efficaces que l'azote, et moins nocifs vis-à-vis des propriétés de l'acier. L'aciérie de Domnarvet adopte alors le dioxyde de carbone dont le craquage à haute température, endothermique, permet de refroidir sensiblement le réfractaire. En 1947-1949, en fin de soufflage, les convertisseurs Thomas de Domnarfvet soufflent ainsi un mélange gazeux contenant jusqu'à 58 % d'oxygène[11].

Mais mélanger l'oxygène avec un refroidissant ne peut être une solution satisfaisante. Pour injecter de l'oxygène pur, il faut momentanément[note 1] renoncer au soufflage par le fond, et assurer le brassage du métal par un autre moyen. Dans ce contexte, la rotation du convertisseur s'impose comme une des rares configurations techniquement réaliste et compatible avec une injection d'oxygène par une lance[6].
Les essais d'un convertisseur rotatif commencent à Domnarvet en 1948[12] avec un prototype d'une capacité interne de 3 tonnes, puis un pilote de 15 tonnes. Le premier démonstrateur industriel, de 30 tonnes, est construit en 1954 et est opérationnel en 1956[13].
Ce convertisseur est appelé « Kaldo », un mot-valise, construit à partir du nom de son inventeur, le professeur Bo Kalling, et de l'usine qui a développé et industrialisé le procédé, la Domnarvets Jernverk. Il se révèle être un succès technique. La possibilité de jouer sur la vitesse de rotation et l'inclinaison de la lance apporte une flexibilité unique. Notamment, grâce à la rotation, la décarburation n'a plus à assurer le brassage du bain et l'injection d'oxygène peut être moins violente. L'oxygène, qui se répand alors dans la cornue, brûle le monoxyde de carbone en dioxyde de carbone, apportant une chaleur supplémentaire. Cette postcombustion peut être utilisée pour refondre des ferrailles, mais le gaz ainsi brûlé ne peut plus être récupéré comme combustible. La complexité mécanique due à la rotation est en partie compensée par l'absence d'installation de récupération des gaz[13].
Adoption du procédé

Les sidérurgistes lorrains, dont le minerai local, la minette, est riche en phosphore, s'intéressent de près au procédé. Convaincus par la nécessité de passer au convertisseur à l'oxygène, ils sont, en 1960, à l'origine du deuxième convertisseur Kaldo. Celui-ci, installé à l'usine sidérurgique de Florange, représente un saut capacitaire notable par rapport à son aîné : il peut affiner 110 tonnes de fonte phosphoreuse[5]. Il s'agit aussi du plus gros convertisseur à l'oxygène pur présent en Lorraine. Sa capacité est par la suite progressivement augmentée jusqu'à 140 tonnes[14].
Dans les années suivantes, le procédé est systématiquement évalué comme une alternative au procédé LD et à ses dérivés. Dès 1965, 10 usines utilisent le procédé Kaldo, en France, Suède, États-Unis, Japon et surtout au Royaume-Uni. Les capacités des nouveaux convertisseurs se situent entre 50 et 140 tonnes[15]. Mais l'avenir du procédé semble déjà compromis : dès 1967, le métallurgiste James Albert Allen estime que « Avec une plus grande consommation de capitaux, des problèmes techniques et une consommation en réfractaire plus élevée, il apparaît plutôt douteux qu'il puisse rivaliser efficacement avec les procédés LD, LD-AC ou leurs évolutions[16]. »
Pourtant, en 1969, « D'autres derviches métallurgiques devaient succéder […], notamment les deux Kaldo de 240 tonnes de Sacilor à Gandrange[5]. » Ces énormes engins de 1 000 tonnes qui tournent à 30 tr/min sont deux fois plus gros que n'importe quel autre convertisseur Kaldo ! Mais deux ans plus tard, deux convertisseurs OLP de 240 tonnes sont mis en service dans la même aciérie alors que le troisième Kaldo prévu est annulé. La course à la taille, censée favoriser les économies d'échelle, a tué le procédé au lieu de le sauver : la limite technologique est atteinte, les coûts augmentent avec les dimensions alors que c'est l'inverse qui était escompté[17].
Adaptation aux métaux non ferreux
En 1958, soit deux ans après la mise en service industrielle du premier Kaldo sidérurgique de 30 tonnes à Domnarvet, l'entreprise canadienne Inco commence à évaluer la déclinaison de ce procédé à la métallurgie extractive du nickel. Elle envoie quelques ingénieurs en Suède pour explorer la conversion à l'oxygène pur de la matte de nickel avec le prototype originel de 3 tonnes. Tous leurs essais ayant réussi, Inco construit un convertisseur expérimental de 7 tonnes dans son centre de recherche de Port Colborne[18]. En Europe, une démarche similaire est entreprise par un producteur belge de cuivre, La Metallo-Chimique, qui construit un four Kaldo dans les années 1960[19] et brevète en 1970 l'affinage de cuivre recyclé[20].
Si La Métallo-Chimique semble la première entreprise à utiliser un kaldo industriel de 70 tonnes[note 2] pour l'affinage des métaux non ferreux, c'est Inco qui, par la mise en service en 1971 de deux convertisseurs de 50 tonnes à Copper Cliff (Grand Sudbury), lance véritablement l'utilisation du Kaldo dans la production des non ferreux. Cette adaptation est renommée TBRC (pour Top Blown Rotary Converter). Elle structure la stratégie d'Inco et s'avère un succès : en 1979, ces deux convertisseurs ont déjà élaboré un million de tonnes de nickel[18], et produisent encore, 45 ans après leur mise en service[21].
Très semblables aux kaldos, les convertisseurs TBRC intègrent le fait que l'oxydation des mattes étant beaucoup moins exothermique que l'oxydation de la fonte[note 3], la lance à oxygène peut être remplacée par un brûleur oxygène-gaz naturel[24]. L'aptitude des convertisseurs TBRC à réaliser successivement la fusion et l'oxydation d'une charge métallique est immédiatement explorée par Inco dans son convertisseur expérimental de Port Colborne. Cet outil de recherche confirme les avantages de l'affinage à l'oxygène dans la métallurgie extractive du cuivre, et positionne le TBRC comme un outil capable de traiter n'importe quelle matte cuivreuse complexe[18]. Mais l'affinage avec le TBRC reste un procédé lent et coûteux : l'utiliser pour la production de cuivre blister à partir de minerai est un luxe. Le convertisseur rotatif ne se justifie que lorsqu'il s'agit de traiter des minerais très complexes, ou de recycler des déchets riches en métaux précieux[25],[26].
En 1976, l'entreprise suédoise Boliden AB met en service le premier TBRC produisant du plomb. L'extraction de ce métal nécessite une étape supplémentaire consistant en une réduction, qui se déroule après la fusion et l'oxydation de la charge[27]. Cette réduction est obtenue en brûlant un combustible riche en carbone (coke de pétrole, poussier de coke, etc.) dans le convertisseur, de manière à y créer une atmosphère réductrice riche en CO tout en apportant de la chaleur[24],[26]. Initialement dédié à l'extraction du plomb contenu dans les poussières issues de la production de cuivre, le TBRC de Boliden devient en 1980 un outil polyvalent, recyclant soit des déchets électroniques contenant du cuivre, soit des déchets riches en plomb[27].
En 1978, la fonderie d'étain de Texas City met en service un TBRC entièrement dédié la fusion réductrice de minerais concentrés de cassitérite. Tout comme pour le plomb, il s'agit de réaliser une oxycombustion qui apportera la chaleur et les gaz réducteurs nécessaires à la désoxydation du dioxyde d'étain. À la fin de la fusion réductrice, l'étain métallique est coulé. Mais les scories restant dans le convertisseur contiennent encore une quantité non négligeable d'étain combiné avec le fer[28]. La méthode de retrait de cet étain scorifié, mise au point en 1974 par La Métallo-Chimique[19], consiste en une addition de soufre (soufre pur ou pyrite) qui, en se combinant à l'étain, permet aux sulfures d'étain de s'échapper sous la forme gazeuse[28]. Les similitudes entre les métallurgies extractives du plomb et de l'étain, qui nécessitent toutes deux une fusion réductrice, ont popularisé la production d'alliages plomb-étain issus du recyclage de déchets avec un TBRC[25],[28].
Notes et références
Notes
- Le convertisseur à l'oxygène à soufflage par le fond ne sera mis au point que dans les années 1970, avec les procédés de type OBM (Oxygen-Bottom Maxhütte).
- Il est difficile de déterminer la date précise de mise en service du premier Kaldo de La Metallo-Chimique. Le convertisseur rotatif y a été adopté pendant les années 1960 pour se généraliser en 1974[19], mais le premier brevet (n° CA979224A) ne date que de 1970. Celui-ci traite de principes généraux sur l'affinage de métaux non ferreux, tout en évoquant des cas industriels relatifs à un convertisseur de 70 tonnes. Par ailleurs, ce brevet, comme les suivants, est déposé uniquement au Canada et aux États-Unis. Il vise donc à éviter tout blocage de la part du concurrent Inco, dont les brevets pourraient gêner une pratique discrètement mise au point[20].
- L'affinage de la fonte au convertisseur est facile car la combustion des éléments indésirables est fortement exothermique : l'oxydation du silicium et du carbone y produit respectivement 32,8 et 10,3 kilojoules par kilogramme[22]. À l'inverse, pour affiner une matte de cuivre, il faut d'abord dissocier le fer du soufre, ce qui consomme 6,8 kilojoules par kilogramme de FeS, avant que leur oxydation, qui ne produit, respectivement, que 5,9 et 9,1 kJ/kg, puisse commencer[23].
Références
- (en) F. Wallner et E. Fritz, « Fifty years of oxygen-converter steelmaking », Revue de Métallurgie, no 10, , p. 825-837
- H. Lecompte, Cours d'aciérie, Éditions de la Revue de métallurgie, , 309 p.
- (en) Donald Garmonsway, « A survey of oxygen steelmaking », New Scientist, no 244, , p. 153-155 (lire en ligne)
- (en) D. J. O. Brandt, « British steelmaking today and tomorrow », New Scientist, vol. 2, no 38, , p. 14-17 (lire en ligne)
- Olivier C. A. Bisanti, « Un siècle d'oxygène en sidérurgie », Soleil d'acier,
- Leroy et al., « Soufflage d'oxygène pur par le procédé LWS », La revue de métallurgie,
- (de)Roman Sandgruber, « Das LD-Verfahren erobert die Welt (Les LD conquièrent le monde) », Oberösterreichische Nachrichten,
- Allen 1967, p. 196
- Allen 1967, p. 202
- (en) James Albert Allen, Studies in Innovation in the Steel and Chemical Industries, Manchester University Press, , 246 p. (ISBN 0-678-06790-2 et 978-0678067901), p. 138
- Kalling et al., « Emploi d'oxygène-acide carbonique au lieu d'air pour le soufflage final dans le procédé Thomas », La revue de métallurgie,
- [PDF](es) Bo Kalling et Folke Johansson, « Procedimiento Stora Kal-Do de fabricación de acero con oxígeno en aparato rotatorio », dans Problemas de la industria siderúrgica y de transformación de hierro y acero en América Latina, vol. 2, Organisation des Nations unies, (lire en ligne), p. 86-88
- (en) B.P. Bhardwaj, Steel and Iron Handbook, Niir Project Consultancy Services, , 472 p. (ISBN 978-93-81039-30-4, lire en ligne), p. 302-313
- Monique Thouvenin, « De WENDEL-SIDÉLOR à SACILOR-SOLLAC : 1968-1980. 13 années de mutations difficiles en Lorraine. », Revue Géographique de l'Est, vol. 21, no 1, , p. 37-63 (lire en ligne)
- Allen 1967, p. 141
- Allen 1967, p. 140
- [PDF]Michel Freyssenet, La sidérurgie française 1945-1979 : L'histoire d'une faillite. Les solutions qui s'affrontent, Paris, Savelli, coll. « Documents critiques », , 241 p. (ISBN 978-2-85930-030-2, OCLC 417353871, notice BnF no FRBNF34648522, présentation en ligne, lire en ligne), p. 81-82
- (en) Paul E. Queneau et Samuel W. Marcuson, « Oxygen Pyrometallurgy at Copper Cliff—A Half Century of Progress », The Minerals, Metals & Materials Society, (lire en ligne)
- « Historique de Metallo Chimique N.V. »
- (en) « Process for recovering copper from copper-bearing materials (CA 979224 A) »
- (en) « Nickel refinery in Canada optimizes the process of rotary converter exchange », Vale,
- Adolf Ledebur (trad. Barbary de Langlade revu et annoté par F. Valton), Manuel théorique et pratique de la métallurgie du fer, Tome I et Tome II, t. 2, Librairie polytechnique Baudry et Cie éditeur, [détail des éditions], p. 472
- Paul Louis Weiss, Le Cuivre : Origine, Gisements, Propriétés physiques et chimiques, Métallurgie… Marché du cuivre, Principales applications… Alliages industriels, J.-B. Baillière et fils, , 344 p. (ASIN B0019TU3SK, lire en ligne), p. 191-193
- Pierre Blazy et El-Aid Jdid, « Pyrométallurgie et électroraffinage du cuivre - Pyrométallurgie », dans Techniques de l'ingénieur, Éditions techniques de l'ingénieur (lire en ligne)
- BREF Industries des métaux non ferreux
- (en) Lennart Hedlund, « Lead and copper recycling in the Boliden Kaldo », EMC'91: Non-ferrous metallurgy - Present and future, Elsevier, , p. 293-298 (ISBN 1851667156, lire en ligne)
- (en) « Rönnskär's history », Boliden AB
- Jacques de Cuyper, « Métallurgie et recyclage de l’étain - Traitements métallurgiques », dans Techniques de l'ingénieur. Élaboration et recyclage des métaux, Éditions techniques de l'ingénieur,
Voir aussi
Articles connexes
- Portail de la production industrielle
- Portail de la chimie