Four à arc électrique
Un four à arc est un type de four électrique utilisé en métallurgie et créé par Ferdinand Frédéric Moissan (Henri)[1]. Il utilise l'énergie thermique de l'arc électrique établi entre une (ou plusieurs) électrode(s) de carbone et le métal pour obtenir une température suffisante à sa fusion.

De petite (environ une tonne) ou grande capacité (jusqu'à 400 t), il est principalement utilisé pour la production d'acier liquide (environ 35 % de la production mondiale) et aussi pour le recyclage des métaux (par exemple pour récupérer le zinc de poussières et déchets métallurgiques) (procédé appelé Electric Arc Furnace Dust (EAFD) par les anglosaxons).
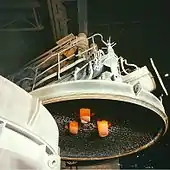
Des fours à arc miniatures sont utilisés dans certains laboratoires de recherche. Certains fours sont utilisés pour des réactions entre solides ou entre phases gazeuses.
On le retrouve dans d'autres secteurs, comme celui de l'odontologie, avec des capacités de quelques dizaines de grammes.
Histoire
Premiers développements
Sir Humphry Davy a effectué une démonstration expérimentale en 1810.
Pinchon a tenté de construire un four électrothermique en 1853 ; en 1878-79, Sir William Siemens a déposé un brevet pour un type de four à arc.
Les premiers fours à arc électrique ont été mis au point par Paul Héroult, en France, près de Grenoble, qui dépose son premier brevet en 1887[2]. Non loin de là, à Venthon, Paul Héroult développe le four à arc pour étudier la métallurgie du vanadium et d'autres ferroalliages dès 1898. Dans la vallée de la Romanche, Keller démarre l'électrochimie à partir de 1902.
Le four électrique de Héroult va rapidement s'imposer comme outil incontournable de la fabrication de ferrochrome, en supplantant rapidement le cubilot. Son avantage décisif apparait lorsque Héroult, en remplaçant le carbone du matériau réfractaire du creuset par de la chromite, parvient à obtenir un ferrochrome d'une teneur en carbone inférieure à 5 %. La fabrication au four à arc rencontre un très grand succès, divisant le coût du ferrochrome par presque trois[2], et permet le développement des aciers inoxydables.
En 1907, des fours sont construits dans une usine aux États-Unis pour une utilisation industrielle. Ils étaient essentiellement destinés à la production d'aciers spéciaux fortement alliés, comme les aciers rapides ou de grande pureté, comme ceux destinés à fabriquer des ressorts en acier. Ainsi, en 1922, Jacques René Levainville explique que :
« Le Comité des forges a calculé qu'en donnant au coke un pouvoir de 7 000 calories et un prix de 25,50 F la tonne (prix d'avant guerre), le prix de revient des 1 000 calories était de 0,009 5 F au haut fourneau et de 0,019 0 F au four électrique, soit un écart de 100 p. 100. Le four électrique, comme appareil sidérurgique, ne garde sa supériorité que dans des cas très spéciaux : en Suède, où les installations des chutes reviennent fort peu cher, en France, pendant les hostilités, quand la valeur du prix de revient disparaissait devant la nécessité d'une fabrication rapide. Cependant le four électrique demeure l'appareil le plus perfectionné pour l'épuration des fontes ou la fabrication des aciers spéciaux[3]. »
— J. Levainville, L'Industrie du Fer en France
Le « Stessano electric furnace » est un four à arc tournant (pour mélanger le bain en fusion). Le Girod furnace est proche du four de Héroult.
Essor moderne de l'aciérie électrique
Les fours à arcs ont été utilisés lors de la Seconde Guerre mondiale pour la production d'alliages d’acier, mais ce n’est qu’ensuite que la fabrication de l'acier électrique s'est vraiment développée, encouragée par le faible coût d'investissement (environ 140 à 200 dollars par t de capacité installée annuelle, comparativement à 1000 dollars par t pour une aciérie classique). De tels fours ont donc été utilisés dans l’Europe ravagée par la guerre où la ferraille de récupération était abondante, faisant naître un type d'aciérie capable de rivaliser avec les grands sidérurgistes des États-Unis, tels Bethlehem Steel et US Steel.
Quand Nucor - maintenant l'un des plus grands producteurs d'acier des États-Unis[4] - a décidé d'entrer sur le marché des produits longs, en 1969, il a construit un four à arc, bientôt suivi par d'autres fabricants.
Actuellement, la filière de production traditionnelle "haut-fourneau - convertisseur à oxygène" s'est de plus en plus cantonnée au marché des "produits plats" - tôle d'acier et plaques d'acier où la pureté chimique des alliages est essentielle. Cependant, en 1987, Nucor a décidé de s'implanter dans le marché des produits plats, toujours en utilisant des fours à arc[5].
Autres utilisations industrielles
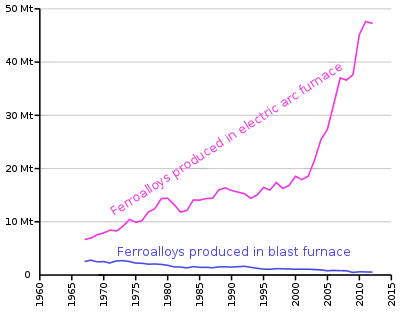
Les fours électriques restent bien sûr très utilisés dans la fabrication de ferroalliages comme le ferrochrome, le ferromanganèse, le ferrosilicium...
On l'utilise également pour l'obtention de métaux purs :
- manganèse en remplacement du haut fourneau. Actuellement, 70 % de la production de manganèse est issu de la filière électrique[6].
- plomb où le processus électrique représentait 71 % de la production en 1992[7], le reste étant issu de haut-fourneaux.
Enfin, le carbure de calcium (carburant de la lampe à acétylène) est également produit dans des fours à arc.
Fonctionnement
Principe
Dans une enveloppe réfractaire (non-fermée pour en évacuer les vapeurs), une forte tension électrique est appliquée entre des électrodes (graphite-carbone) et le métal à faire fondre. Cette tension fait jaillir un arc électrique. Les câbles électriques, l'enveloppe, le toit (ou la coupole) et certains éléments sont refroidis à l'eau ou un autre fluide caloporteur.
La température engendrée par l'arc dépasse 1 800 °C et peut atteindre les 3 600 °C. Une zone plus froide persiste entre les électrodes, problème qui est généralement résolu par des brûleurs à gaz + oxygène ou un brassage électro-magnétique du métal en fusion.
Certains fours fonctionnent en courant continu et ne sont alors équipés que d'une seule électrode.
Des ouvertures ou le basculement du four permettent de récupérer le métal fondu et le laitier.
Consommation d'énergie
Elle est très variable selon l'âge et la qualité du four et selon les matériaux qu'on y entre.
Une tonne d'acier pour être produite dans un four à arc électrique nécessite en théorie environ 440 kWh. Le minimum théorique requis pour faire fondre une tonne de déchets d'acier est 300 kWh (point de fusion 1 520 °C). Fabriquer de l'acier avec un arc électrique n'est donc économique que là où il y a abondance d'énergie électrique, avec un réseau électrique stable et bien développé.
Qualité
Les fours électriques utilisés en sidérurgie ont l'intérêt de recycler les ferrailles. Le risque d'entraîner la présence d'impuretés non désirables est minime et parfaitement maitrisé par l'aciériste parce que le choix des ferrailles permet d'éliminer les ferrailles suspectes (telles que ferrailles de chiffonnier). La qualité des ferrailles peut être choisie en fonction des exigences sur le produit à obtenir. L'aciériste peut utiliser des lots homogènes dont il connait l'histoire, par exemple chutes de fabrication au laminage. Si une anomalie se produisait elle serait détectée par les premières analyses faites dès la fusion. Actuellement les produits pour lesquels les exigences sont les plus grandes, telles que pièces pour le nucléaire et l'aéronautique, sont issus de coulées au four électrique, complétées éventuellement par des traitements (dégazage) par le vide et des traitements en poche chauffante. Ainsi le four électrique est loin d'être réservé aux produits les moins exigeants. Il est au contraire utilisé pour produire les aciers de plus haute qualité.
Notes et références
- (en) Oleg D. Sherby, Jeffrey Wadsworth, Donald R. Lesuer et Chol K. Syn, « Revisiting the Structure of Martensite in Iron-Carbon Steels », MATERIALS TRANSACTIONS, vol. 49, no 9, (ISSN 1345-9678 et 1347-5320, DOI 10.2320/matertrans.MRA2007338, lire en ligne, consulté le )
- (fr) Olivier Bisanti, « 101 ans de Four Héroult », sur http://soleildacier.ouvaton.org/, (consulté le )
- Jacques René Levainville, L'Industrie du Fer en France, Paris, Armand Colin, coll. « Armand Colin » (no 19), , 210 p. (ASIN B0000DRHCW, lire en ligne), p. 164-165
- www.worldsteel.org
- Preston, R.,American Steel. Avon Books, New York, 1991
- (en) « Description du Manganèse sur SfC.fr », Manganèse (consulté le )
- (en) « Description du Plomb sur SfC.fr », Plomb (consulté le )
Voir aussi
Bibliographie
- H. W. Beaty (ed), Standard Handbook for Electrical Engineers, 11e éd., McGraw Hill, New York, 1978 (ISBN 0-07-020974-X)
- J.A.T. Jones, B. Bowman, P.A. Lefrank, Electric Furnace Steelmaking, in The Making, Shaping and Treating of Steel, R.J. Fruehan, Editor. 1998, The AISE Steel Foundation: Pittsburgh. p. 525-660
Articles connexes
- Aciérie électrique
- Four à induction, autre type de four électrique (« Four Kjellin »).
Liens externes
- (en) Lien vers le module de formation du site de SteelUniversity.org
- (en) Recognition of first foundry as historical site
- (en) Home made small scale arc furnace using a welder
- Portail de la chimie
- Portail de la production industrielle
- Portail de l’énergie