Cokerie
Une cokerie est une usine réalisant la synthèse de coke et de gaz manufacturé à partir de charbon par un procédé de distillation à sec. Les composants volatils du charbon pyrolysés, libérés par chauffage à une température comprise entre 900 °C et 1 400 °C sont généralement aspirés et récupérés ; mais il existe aussi des cokeries où les composants libérés sont brûlés : on parle dans ce cas de procédé de récupération de chaleur (Heat Recovery). Il se forme alors à la surface du coke obtenu une couche de cendres[1]. Le dégazage du charbon confère au coke une porosité très recherchée. Les gaz sont décomposés par condensation fractionnée en goudrons d'hydrocarbure, acide sulfurique, ammoniac, naphtalène, benzol et gaz de coke : ces produits sont ensuite purifiés dans d'autres réacteurs chimiques. L’Allemagne maintient (en 2010) encore cinq cokeries en activité pour les besoins de son industrie nationale.
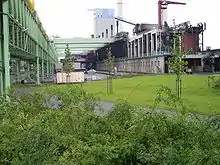
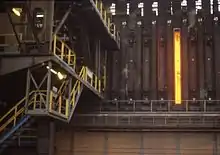
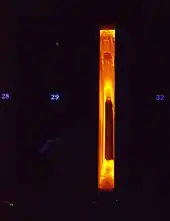
Le coke est surtout recherché pour produire de la fonte (sidérurgie) dans les haut-fourneaux, et cela demeure sa principale utilisation aujourd'hui. Le dégazage permet de réduire considérablement sa teneur en soufre, ce qui permet à l'industrie sidérurgique de produire des fontes de meilleure qualité, tout en étant moins polluante. Les cendres de coke sont, hormis cela, à peu près de même composition que celle de la houille ordinaire.
Histoire et principe
Dans les débuts de la sidérurgie, on utilisait exclusivement le charbon de bois dans l'élaboration des minerais[2]. Les charbons fossiles bruts (lignite et houille) ou le bois non carbonisé sont impropres à la métallurgie du fer, car la teneur en impuretés ne permet pas d'atteindre une température suffisante pour produire de la bonne fonte. La demande en charbon de bois, tiré de charbonnières au fonctionnement très voisin des cokeries modernes, a entraîné des défrichements massifs qui ont défiguré définitivement des régions entières (par exemple la forêt d'Ashdown en Angleterre). Ce n'est qu'au XVIIIe siècle qu'on a imaginé de purifier la houille naturelle au moyen de cokeries. Le nouveau combustible évinça bientôt entièrement le charbon de bois, rendit possible la production de masse de la fonte et donc le chemin de fer.
Le chauffage de charbon en absence d'air donne le coke, un combustible particulièrement riche en carbone, plus pur et de meilleure qualité que la houille naturelle. Le contrôle du procédé permet d'atteindre des performances particulières sur les propriétés suivantes :
- teneur en eau ;
- teneur en cendres ;
- teneur en soufre ;
- taille des grains ;
- dureté ;
- indice de friabilité.
Le coke est le plus souvent employé dans les hauts-fourneaux et en fonderie. L'une des propriétés les plus importantes du coke de haut-fourneau est sa dureté, qu'il conserve même aux hautes températures : ainsi, tout en servant de combustible, il assure la stabilité de l'empilement de minerais ferreux et de fondant, alors que de la houille ordinaire cuirait et gênerait l'oxygénation du mélange.
Description
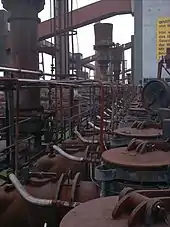
Les fours à coke
Le four à coke est l'élément central d'une cokerie. Les fours horizontaux, qui sont les plus utilisés (ils conviennent au suivi des différentes étapes d'extraction) se présentent comme des compartiments étroits (env. 50 cm de largeur), mais hauts et profonds de plusieurs mètres. Les compartiments modernes offrent un volume allant jusqu'à 100 m3 (par ex. 0,5 × 6 × 32 m). En règle générale, ces fours sont mis en batterie, séparés par les injecteurs de gaz brûlés entre 1 200 et 1 400 °C qui assurent le maintien de la température interne. Ces gaz proviennent des évacuateurs de fumée, qui assurent par la même occasion la récupération de chaleur. Pour peu que l'on soit sur le site d'une centrale sidérurgique, le gaz de haut fourneau peut servir aussi pour le chauffage des étages inférieurs, où il est mélangé au gaz s'exhalant du grillage du charbon. Toutes les demi-heures, le chauffage de la batterie de fours alterne entre les côtés et le haut, afin d'assurer une isotropie du grillage du charbon.
Au bout d'une phase initiale d'environ trois mois suivant sa mise en service, le système de chauffe d'une cokerie tourne en continu. Un chauffage trop rapide ou une interruption trop brutale du chauffage s'accompagne de contraintes thermiques telles que les fours sont irréparablement endommagés.
Les fours, comme les hauts fourneaux, sont garnis intérieurement de couches réfractaires de chamotte ou de silicates. Chaque four possède trois ouvertures : les portes avant et arrière, à peu près aussi larges que le four lui-même, et la trappe de remplissage/évacuation en partie supérieure. Le réglage des couches de charbon par assises horizontales à l'intérieur du four est assuré par un râteau oléo-hydraulique.
La couverture
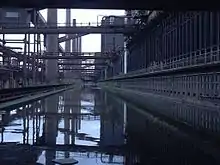
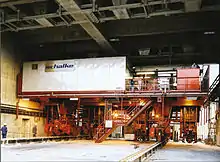
La couverture n'est pas seulement la dalle de fermeture de la batterie de four : c'est par là que le pont roulant transportant la benne à charbon vient charger chaque four individuellement. Pour l'ouvrier chargé de cette opération, l'exposition aux risques est maximum : poussières, chaleur et flammes rendent la tâche des plus périlleuses.
Bac à charbon
Selon le type de four, les bacs à charbon se trouvent soit au dessus de la batterie de fours, soit à une extrémité. Chaque bac contient la quantité de charbon nécessaire au remplissage d'un four. Ces bacs contiennent un mélange de charbons spécialement choisis en vue de la qualité de coke à produire, préalablement criblé ou pulvérisé.
Dégrilleur
Le dégrilleur est un chariot mobile sur des rails, placés le long d'un des côtés de la batterie de fours. Il est prévu pour sortir des fours les briquettes de coke et les acheminer sur le site d'élaboration. Il est équipé d'un bras articulé, comprenant souvent deux articulations, capable de balayer la totalité de la longueur de la batterie de fours. La centrale hydraulique se trouve à la base de ce bras articulé. L'allée devant les fours le long des rails est appelée allée maîtresse ; elle doit permettre le passage simultanée de l'ouvrier chargé de la fermeture des portes, que celui du contremaître.
- Dégrilleur à coke de Schwelgern, Forges de Gelsenkirchen-Schalke.
- Nacelle mobile de la cokerie Prosper.
- Dégrilleur à coke avant...
- ...et après son introduction dans le four.
Déroulement des opérations
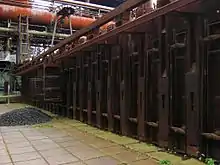
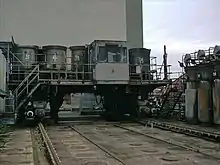
- Alimentation du four en charbon, avec mélange, broyage et compactage
- Ouverture de la trappe d'alimentation par un pont roulant en partie haute du four
- Largage du charbon dans un seul four
- Selon le type de four ou la qualité du charbon, piquage du charbon
- fermeture étanche (à l'air) du four
- Chauffage
- Suivent le dégazage et l'attente d'une porosité suffisante.
- Ouverture des portes d'extrémité du four
- Récupération du coke
- Extinction et alimentation simultanée du four pour le cycle suivant
Une fois que le four est plein, l'enfourneuse repart vers la trémie à charbon et charge le four suivant. Les cycles sont minutés de telle façon que toutes les deux minutes un nouveau four puisse être mis en route. Les parois des fours sont continuellement chauffés. Selon les propriétés des briques de coke et la taille du four, la cuisson dure entre 15 et 30 heures.
- Enfourneuse de la cokerie Schwelgern, aux Forges de Gelsenkirchen-Schalke.
- Refroidisseur de la cokerie Schwelgern
- Hotte du refroidisseur de la cokerie Prosper
- Chargement du wagon (ou coke-car)
- Départ vers le refroidisseur
Extinction du coke
Le refroidissement du coke doit être particulièrement rapide, car dès la mise en contact avec l'air ambiant, le coke, du fait de sa température extrêmement élevée, commence à se consumer.
- Coke incandescent en cours d'acheminement vers le refroidisseur.
- Extinction du coke par voie humide.
- Le coke éteint est conservé quelque temps dans la trémie pour contrôle de qualité.
Il y a deux voies pour refroidir le coke :
Refroidissement par voie humide
- Ce procédé nécessite env. 2 m3 d'eau par tonne de coke.
- La chaleur est perdue.
- Près d'un tiers de l'eau se dissipe en vapeur.
- La purification de cette vapeur, contaminée en acide sulfurique, poussières et gaz à l'eau reste problématique.
En 1986 on relevait au cours du refroidissement entre 200 g et 2 kg d'impuretés solides par tonne de coke. Grâce au procédé moderne dit (Coke Stabilizing Quenching), cette quantité a été ramenée à 10 à 15 g/t.
Refroidissement à sec
Il est conduit le plus souvent avec de l'azote liquide, choisi comme gaz inerte.
- Cette technique permet des économies d'énergie,
- évite l'emprunt d'eau au milieu naturel,
- dissémine moins de poussières.
- La teneur en eau finale étant plus faible, on obtient un coke de qualité supérieure.
- Le procédé est en revanche coûteux en investissement et en entretien ; cet aspect est toutefois contesté par certains experts et entrepreneurs. C'est surtout le cas pour les récupérations d'énergie, qui réduisent les coûts annuels d'exploitation. En Chine, le second producteur mondial d'acier, Nippon Steel Corporation, estime que ses investissements dans le refroidissement par voie sèche lui procurent entre 20 et 33 % d’économies[3].
La phase gazeuse
Vers le milieu du XIXe siècle, les industriels prirent conscience de la valeur des gaz dégagés pour l'industrie chimique. Les distillateurs assurant le lavage des gaz et la séparation de leurs composants sont souvent montés à même le socle de la batterie de fours et connectés par des conduites étanches. Les gaz sont aspirés par des ventilateurs qui doivent cependant maintenir une surpression comprise entre 2 mbar et 5 mbar, afin d'éviter absolument tout risque d'explosion du four consécutif à l'arrivée d'air extérieur. Si le ventilateur est bloqué, il se forme une torchère.
Le gaz de houille est d'abord refroidi et finalement lavé dans un absorbeur ; puis les produits de la condensation sont séparés et expédiés vers les différentes filières[4] :
sous-produits
- Goudrons
- Benzol
- Soufre
- Ammoniac
- Sulfate d'ammonium, et plus rarement du nitrate d'ammonium (engrais)
- acide sulfurique
- Phénols alcalins
Les cokeries aujourd'hui (2005)
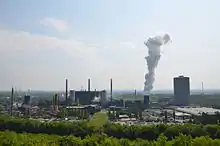
Les cours mondiaux du coke explosent. Entre 2002 et 2004, la demande en acier a fait bondir le cours du coke produit en Chine de 80 $ à près de 350 $, soit un prix plus que quadruplé, et une hausse trois fois supérieure à celle, simultanée, de l'acier lui-même.
Parallèlement les Chinois ont démantelé la cokerie moderne de Kaiserstuhl à Dortmund dans la Ruhr pour la reconstruire en Chine[5]. La dernière usine d’Allemagne à refroidissement par voie sèche n'a pu prendre le relais, puisque le groupe Thyssenkrupp a regroupé ses usines de fonte et d'acier à Dortmund et à Duisbourg.
Les trois dernières cokeries en activité de la Ruhr : la cokerie ArcelorMittal Prosper à Bottrop, la cokerie Carbonaria / ThyssenKrupp à Duisbourg-Schwelgern et celle de la centrale thermique de Duisburg-Huckingen, sont depuis 2010 aux limites de leurs capacités. La déclaration d'utilité publique d'extension de la cokerie de Duisbourg-Huckingen pour HKM (Hüttenwerke Krupp Mannesmann), accordée le 3 juin 2005 par les autorités du district de Düsseldorf, a été confirmée le 13 janvier 2006. La cokerie a été inaugurée le 29 mars 2014.
Au mois de décembre 2005, la remise à niveau de la cokerie centrale de la Sarre (Zentralkokerei Saar GmbH), à Dillingen, a été approuvée. Il s'agit de construire une troisième batterie de fours entièrement neuve. Elle permettra à terme d'arrêter l'exploitation de la batterie no 1, qui sera reconstruite. La batterie no 2 sera supprimée.
En France, en , 6 cokeries sont en service : 3 cokeries du groupe sidérurgique Usinor à Serémange, Dunkerque et Fos-sur-Mer, 2 des Charbonnages de France à Drocourt et Carling, et celle, en sursis, de Pont-à-Mousson[6],[7]. En , après la fermeture de la cokerie de Serémange[8], il ne reste plus que celles de Dunkerque et Fos-sur-Mer.
La Carling a été fermée en octobre 2009.
- La cokerie Schwelgern GmbH.
Politique industrielle
Compte tenu de la hausse soutenue du cours du coke, plusieurs partisans de cette industrie ont représenté aux autorités allemandes qu'il serait rentable de rouvrir certains puits de charbon. Il existe ainsi un projet entièrement sur fonds privés d'ouvrir une mine au nord de Hamm, qui se heurte toutefois à l'importance de l'investissement[9]. Les sceptiques redoutent que des investissements dans ce secteur au cours du cycle économique actuel n'aient des conséquences sur les finances publiques en cas de pénurie.
Bibliographie
- Handbuch der Gasindustrie, en particulier le tome 1 „Gaserzeugungsöfen“, Dr.-Ing. Horst Brückner et al., éd. R.Oldenbourg, Munich et Berlin (1938)
- Walter Buschman: Zechen und Kokereien im rheinischen Steinkohlenbergbau. Aachener Revier und westliches Ruhrgebiet. Mann, Berlin 1998, (ISBN 3-7861-1963-5)
- Dietmar Osses: Kohle, Koks, Kultur. Die Kokereien der Zeche Zollverein. Stiftung Industriedenkmalpflege und Geschichtskultur, Dortmund (2002?), (ISBN 3-935783-09-4)
- Franz Michael Ress: Geschichte der Kokereitechnik. Glückauf, Essen 1957
- Fritz Schreiber: Entwicklung und gegenwärtiger Stand der Kokereiindustrie Niederschlesiens. Springer, Berlin 1911 (Digitalisé)
- Michael Farrenkopf (éd.): Koks. Die Geschichte eines Wertstoffes, 2 vol. Musée des mines d'Allemagne, Bochum 2003.
Notes et références
- Cf. Uhde, « Competence and know-how by tradition - A new dimension in cokemaking technology » [PDF; 3,9 MB], sur Thyssen-Krupp.
- Cf. Rolf Peter Sieferle, Der unterirdische Wald. Energiekrise und industrielle Revolution., Munich,
- Cf. (en) Prof. Mitsutsune Yamaguchi, « Case Study of Technology Transfer between Japan and China in iron/steel industry » [PDF; 3,3 MB], sur In-session Workshop on Mitigation at SBSTA22, Teikyo University, Japon, .
- Cf. Theo Payer et Wilhelm Baum, « Gasreinigung und Nebenproduktgewinnung » [archive du ] [PDF; 5,0 MB], sur Fischer-Tropsch (consulté le ).
- Cf. Stefan Willeke, « Herr Mo holt die Fabrik – Die modernste Kokerei der Welt zieht von Dortmund nach China », DIE ZEIT, no 40, (lire en ligne).
- Jacques Corbion (préf. Yvon Lamy), Le savoir… fer — Glossaire du haut fourneau : Le langage… (savoureux, parfois) des hommes du fer et de la zone fonte, du mineur au… cokier d'hier et d'aujourd'hui, 5, [détail des éditions] (lire en ligne [PDF]), § Cokerie
- Pascal Ambrosi, « Pont-à-Mousson va fermer une cokerie en Meurthe-et-Moselle », Les Échos, (lire en ligne)
- François Pelleray, « La cokerie d'ArcelorMittal s’éteint à Serémange-Erzange », France Bleu Lorraine Nord,
- wa.de: Pläne für einen Förderstandort Donar gehören endgültig der Geschichte an, 7 février 2013.
Voir aussi
Articles connexes
Liens externes
- (de) Constructeurs de cokeries en Europe et en Amérique du Nord
- La cokerie Schwelgern – Panorama Interactif – disponible en grand format
- Photographies de cokeries
- Portail des sciences des matériaux
- Portail des énergies fossiles