Frein à disque
Le frein à disque est un système de freinage performant pour les véhicules munis de roues en contact avec le sol : automobile, moto, camion, avion, train, vélo tout terrain, etc. et pour diverses machines réclamant des freins performants et endurants.
Pour les articles homonymes, voir Frein (homonymie).
Ce système transforme l'énergie cinétique du véhicule en chaleur qui doit être dissipée le plus rapidement possible.
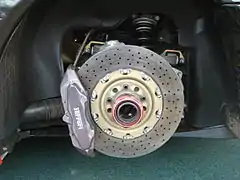
Historique et emploi
Le développement des freins à disque a commencé en Angleterre dans les années 1890.
Le premier frein à disque automobile de type étrier a été breveté par Frederick William Lanchester dans son usine de Birmingham en 1902 et utilisé avec succès sur les voitures Lanchester. Cependant, le choix limité des métaux à cette époque signifiait qu'il devait utiliser le cuivre comme moyen de freinage agissant sur le disque. Le mauvais état des routes à cette époque, des pistes poussiéreuses et rugueuses, entrainait une usure rapide du cuivre rendant le système impraticable[1].
En 1921, la société de motos Douglas a introduit une forme de frein à disque sur la roue avant de ses modèles sportifs à soupapes en tête. Breveté par la British Motorcycle & Cycle-Car Research Association, Douglas a décrit le dispositif comme un «frein à coin novateur (novel wedge brake)» fonctionnant sur une «bride de moyeu biseautée», le frein étant actionné par un Câble Bowden. Des freins avant et arrière de ce type ont été montés sur la machine sur laquelle Tom Sheard a remporté la victoire dans le Senior TT de 1923[2].
Une application réussie a commencé sur les trains de voyageurs de lignes ferroviaires, sur les avions et les chars avant et pendant la Seconde Guerre mondiale. Aux États-Unis, la Budd Company a introduit des freins à disque sur le General Pershing Zephyr pour le chemin de fer de Burlington en 1938. Au début des années 1950, les freins à disque étaient régulièrement appliqués aux nouveaux matériels de trains de passagers.[3] En Grande-Bretagne, la société Daimler a utilisé des freins à disque sur son Automitrailleuse Daimler de 1939, les freins à disque fabriqués par la société Girling (absorbée par Lucas Industries en 1938) étaient nécessaires car dans ce véhicule à quatre roues motrices (4x4) la transmission finale épicycloïdale se situait dans les moyeux de roue et n'a donc laissé aucune place aux freins à tambour conventionnels montés alors.[4]
Chez Argus Motoren en Allemagne, Hermann Klaue (1912-2001) a breveté[5] des freins à disque en 1940. Argus a fourni des roues équipées de freins à disque, par ex. pour l'Arado Ar 96[6]. Le char lourd allemand Tiger I a été introduit en 1942 avec un disque Argus-Werke de 55 cm [7] sur chaque arbre d'entraînement.
Le constructeur automobile américain Crosley est souvent reconnu pour les premiers freins à disque de série automobile. Entre 1949 et 1950, Crosley construit plusieurs modèles (HotShot, Super Sport, Sedan, Station Wagon, Pickup) avec des freins à disque aux quatre roues, puis revient aux freins à tambour. Le manque de recherches suffisantes a causé des problèmes de fiabilité, tels que le collage et la corrosion, en particulier dans les régions utilisant du sel sur les routes d'hiver. Les freins à disque à quatre roues Crosley ont rendu leurs produits populaires pour les courses automobiles dans les années 1950. Leur freinage supérieur les rendait difficiles à battre. Les conversions de frein à tambour pour Hot Shots étaient très populaires.[8] Le disque Crosley était une conception Goodyear-Hawley, avec un type d'étrier moderne, dérivé d'une conception d'applications aéronautiques.[9].
Son mode de fonctionnement est très proche de celui du frein à mâchoire des bicyclettes, qui pince la jante entre deux patins en caoutchouc, mais les matériaux utilisées, pour les automobiles et avions, permettent de bien meilleures fiabilité et endurance.
Aviation
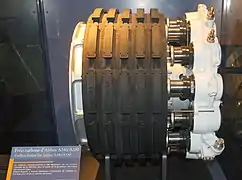
En aviation, ce type de frein étant plus léger, plus facile d'entretien que les autres systèmes et les coûts étant « accessoires » dans ce domaine, il est utilisé depuis très longtemps.
Les avions actuels emploient les freins à disques sous une forme légèrement différente de ceux équipant habituellement les voitures. Le système est en effet constitué d'un empilement « en sandwich » de plusieurs disques, alternés chacun successivement avec un plateau de friction. Les disques sont dotés de cannelures, sur lesquelles sont emboîtées les jantes des roues de l'appareil, alors que les plateaux de friction coulissants sont fixés sur le moyeu de la jambe de train d'atterrissage. Au bout de l'empilement, plusieurs pistons (plus d'une dizaine) sont chargés de presser très fort sur cet assemblage pour faire ralentir puis stopper un appareil à l'atterrissage.
De par sa forme, cet assemblage de plateaux empilés pourrait ressembler de loin à un embrayage automobile.
Automobile
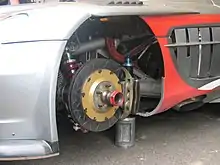
Dans le domaine automobile, on doit à Jaguar le développement, dans les années 1950, du frein à disque pour son Type C, en collaboration avec les ingénieurs de Dunlop. Cette véritable nouveauté allait d'ailleurs constituer l'arme secrète de Jaguar lors de son retour sur le circuit des 24 Heures du Mans, en 1953. Les freins à disque ont ensuite commencé à se généraliser sur les véhicules haut de gamme, avant de s'étendre à tous les véhicules sur le train avant.
La première voiture à adopter les freins à disques à l'avant, de série, fut la Citroën DS en 1955[10] La première voiture équipée de freins à disque sur les quatre roues fut la Renault Dauphine, dans les années 1960. En 2003, Mercedes-Benz innove en proposant des disques de frein renforcés de fibres de céramique sur un de ses modèles, la SLR[11].
Depuis 2014, seules les petites automobiles légères utilisent encore des freins à tambour sur l'essieu arrière (ex: Smart Forfour II ou Renault Twingo III)
Deux-roues
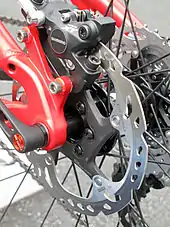
- Motos
Sur les motocyclettes, son utilisation a été rare jusqu'à la Honda CB 750 Four de 1969, qui a imposé le frein à disque à commande hydraulique. Ce type de freinage s'est rapidement généralisé sur les machines de compétition. Il s'est perfectionné en ajoutant des perforations, ou des rainures, dans le disque[12] et en devenant double (à l'avant).
En 2014, les motos de compétition sont équipées de freins en carbone ou en céramique[13].
De nombreux modèles de motos sont munis de deux disques sur la roue avant, pour mieux répartir la force de chaque côté de la fourche afin d'éviter qu'elle ne se vrille, ce qui nuirait à la tenue de route. Le diamètre des disques est un facteur important, entre autres, en compétition, mais l'effet gyroscopique créé augmente lorsque le ratio diamètre/masse en mouvement augmente, ce qui réduit l'agilité.
- Vélos
Actuellement, de nombreux VTT et bicyclettes sont dotés de freins à disque. Cette caractéristique était au départ essentiellement représentative des vélos tout-terrains de compétition, comme les VTT de descente, mais elle tend à devenir accessible à tout le monde, même sur des vélos à moindre coût vendus en grandes surfaces.
Principe et fonctionnement
Le frein à disque est un système utilisant un disque, fixé sur le moyeu de la roue, et des plaquettes, venant frotter de chaque côté du disque. Les plaquettes sont maintenues dans un étrier (frein fixe) ou une chape (frein coulissant), fixés au véhicule. Un ou plusieurs mécanismes poussent sur les plaquettes, en général un ou plusieurs pistons soumis à une pression hydraulique (véhicules de tourisme, commerciaux, poids lourds) ou à un mécanisme lui-même actionné par un actionneur pneumatique (frein de semi-remorque). L'effort ainsi généré provoque le serrage puis le frottement des plaquettes sur le disque. La force de frottement entre les plaquettes et le disque crée le couple de freinage mais aussi de la chaleur, qui doit être évacuée le plus rapidement possible pour éviter une déformation (voire une destruction) du disque.
- Schéma du fonctionnement des freins à disque à étrier flottant
- Frein ouvert.
- Frein partiellement serré.
- Frein complétement serré.
Le système de commande (maître-cylindre) peut être indépendant pour les différents disques ou être couplé avant-arrière par un répartiteur (cas général des voitures et du freinage intégral de certaines motos, comme les Moto Guzzi ou Honda CBR1000F).
Caractéristiques
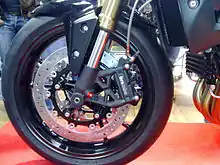
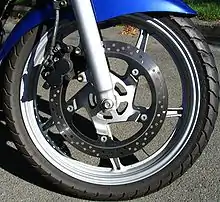
Technologie : étriers fixes ou flottants
Afin d'assurer la pression des plaquettes sur les deux faces du disque, trois concepts de freins existent :
- Frein (ou étrier) fixe
- Les plaquettes sont poussées contre le disque par l'intermédiaire d'un ou plusieurs pistons situés de chaque côté du disque et dédiés à chaque plaquette. Ce concept, permettant d'appliquer une grande force de freinage, est en général utilisé sur des voitures performantes car sa fabrication est coûteuse, notamment à cause de l'étanchéité à réaliser entre les deux chambres hydrauliques qui alimentent les pistons de part et d'autre du disque. Ce système permet, sur les véhicules sportifs, d'obtenir des montages à 4, 6, voire 8 pistons.
- Frein à étrier flottant ou coulissant
- Seule la plaquette intérieure est poussée contre le disque par un ou plusieurs pistons. La pression de la plaquette extérieure contre le disque est réalisée par l'intermédiaire de l'étrier monté sur un système coulissant dans la chape (pièce de fonderie supportant les plaquettes et fixant le frein complet sur le véhicule). C'est le concept le plus répandu. Bien que plus simple de conception, il est moins bien adapté aux véhicules lourds ou rapides que le modèle à étrier fixe. De plus, l'usure des plaquettes est fréquemment asymétrique, la plaquette extérieure (qui n'est pas directement poussée par le piston) ayant tendance à s'user moins vite que l'autre.
- Frein à étrier pivotant
- Dans les années 1960 à 1970, Honda utilise, sur ses motos, un montage à étrier pivotant. Ce montage a l'inconvénient d'user les plaquettes de travers, ce qui induit une efficacité variable au fur et à mesure de l'usure des plaquettes.
Technologie : étriers monoblocs
Les étriers peuvent être construits à l'aide de deux pièces, gauche et droite, assemblées par des vis, ou bien, dans le cas des étriers monoblocs, constitués d'une seule pièce usinée. Les étriers monoblocs sont plus résistants aux déformations et échauffements.
Technologie : fixation axiale ou radiale
La fixation de l'étrier sur la fourche d'une moto peut se faire de deux manières, comme on le voit sur les images ci-dessus :
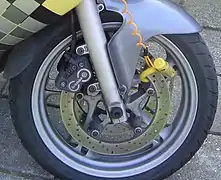
- Fixation axiale
- L'étrier est maintenu principalement par l'une de ses extrémités, vissée sur une patte, elle-même fixée sur la fourche.
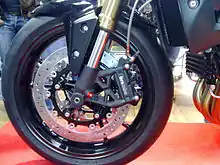
- Fixation radiale
- L'étrier est maintenu par ses deux extrémités, à l'aide d'une monture à deux pattes fixée sur la fourche. Cette fixation est plus rigide que la fixation axiale et garantit la constance des freinages quelle que soit l'usure et l'échauffement.
Matériaux employés

De nombreux matériaux peuvent être utilisés.
- Disques
- Acier inoxydable : assez cher, et n'offrant pas une friction idéale.
- Fonte : bien que ce matériau rouille facilement et soit assez lourd, il est très économique et jouit d'une bonne efficacité à l'emploi. C'est de loin le matériau le plus utilisé.
- Carbone : ce matériau extrêmement léger et endurant coûte très cher et ne fonctionne bien qu'à hautes températures. Il est par conséquent réservé à l'emploi par des véhicules de compétition ou les avions qui en ont un besoin intense pendant une courte periode.
- Céramique : comme le carbone, ce matériau extrêmement léger et endurant coûte cher, mais, à l'inverse de ce dernier, est également efficace à basses températures. Il est également totalement insensible à l'humidité et ne s'oxyde pas. En raison de son prix, il est actuellement essentiellement réservé aux véhicules haut de gamme.
- Plaquettes
Les plaquettes sont généralement formées d'un support en acier, assurant la fixation dans les étriers, sur lequel est fixé par collage un patin en matériau composite, s'usant progressivement au cours de l'utilisation. La composition du patin varie suivant le matériau du disque et suivant les fabricants. L'amiante a été longtemps utilisé dans la composition de ces patins, en raison sa très bonne tenue aux hautes températures, mais il est désormais interdit en raison de sa toxicité (il était libéré dans l'air, et contribuait à la pollution routière), dont en France depuis 1997[14].
Avantages et inconvénients
Qualité du freinage
Par rapport au frein à tambour, le frein à disque a l'avantage d'être plus progressif car il n'est pas « autoserrant », mais il nécessite une plus grande pression pour être efficace. En comparaison, un frein à tambour offre plus de puissance pour un diamètre moindre, car la force appliquée sur les mâchoires s'applique directement à la périphérie du tambour supportant la piste de frottement, ce qui apporte un effet de levier plus important.
La pression que le conducteur exerce sur la pédale de frein est transmise par un système hydraulique, le plus souvent assisté[15], pour réduire la pression que le conducteur doit exercer sur la pédale, afin d'améliorer son confort et la sécurité. Par contre, la commande du frein à main est encore assez souvent mécanique, parfois électrique.
Dissipation de la chaleur
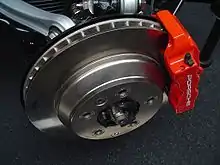
Autre avantage du frein à disque, il dissipe mieux la chaleur que son cousin à tambour. La raison vient de la conception même du système : dans un frein à disque, les deux côtés du disque offrent une grande surface exposée à l'environnement extérieur, et il peut alors se créer un échange thermique efficace avec l'air extérieur. De plus, lorsque le véhicule est en mouvement, la circulation forcée de l'air s'engouffrant à grande vitesse dans les passages de roues améliore encore le refroidissement. Le tambour n'offre aucune de ces caractéristiques, car il est essentiellement une « boîte fermée ». La chaleur s'y accumule facilement et a beaucoup de mal à s'évacuer vers l'extérieur.
L'évacuation de la chaleur est un point crucial dans la conception d'un système de freinage, qu'il soit à disque ou autres. Une chaleur trop élevée, ou mal évacuée, expose à de nombreux risques :
- Déformation du disque : on dit alors qu'il est « voilé ».
- Modification de l'état de surface : l'état de surface du disque est altéré par une surchauffe, il est alors « glacé » et prend une couleur légèrement bleutée. Cette réaction à une chaleur excessive peut être comparée à une trempe ou à un traitement thermique, comme il est fréquent d'en voir dans les industries métallurgiques. Le mordant au freinage diminue.
- Ébullition du liquide de freinage : pour les circuits utilisant un liquide de freinage (cas de toutes les voitures récentes). La température excessive des plaquettes, qui n'arrivent pas à évacuer leurs calories correctement, se transfère via les pistons et l'étrier jusqu'au liquide de freinage, qui se met alors à entrer en ébullition. De petites bulles se forment alors dans le circuit, et comme le gaz est compressible, contrairement au liquide, la force appliquée au circuit de freinage est diminuée et irrégulière.
En utilisant un disque évidé, l'air peut circuler au sein du disque et le ventiler de l'intérieur afin qu'il se refroidisse plus efficacement. On parle alors de disques « ventilés ». Ils sont en fait constitués de deux disques légèrement séparés par un ensemble d'entretoises permettant la circulation de l'air entre ces derniers. Afin d'améliorer le refroidissement, les canaux de refroidissement sont usinés en spirale et dans le sens de rotation, afin de maximiser la quantité d'air aspirée quand le véhicule est en mouvement.
Par rapport à l'acier, la céramique ou le carbone résistent beaucoup mieux à l'échauffement, et offrent donc un freinage plus performant. Ces matériaux sont cependant extrêmement chers.
Évacuation de l'eau
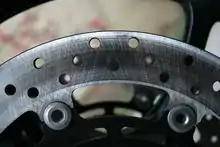
Habituellement, le frein à disque fonctionne à l'air libre, ce qui lui permet d'évacuer la chaleur du freinage par ses deux faces. En revanche, cela l'expose aux projections d'eau, ce qui provoque un retard au freinage lorsqu'il est mouillé. Il se crée en effet une fine pellicule d'eau entre la surface du disque et celle de la plaquette, et le liquide n'étant pas compressible, la plaquette met un peu de temps à venir s'appuyer contre le disque.
Pour évacuer le plus rapidement l'eau qui se pose sur les disques en cas de pluie, on trouve des petits trous à la surface des disques, dont le rôle est de rompre le film liquide créé par l'eau. Ces disques, dits « perforés », sont très présents sur les motos et sur de nombreuses voitures de sport. Ils ont cependant l'inconvénient de diminuer la puissance de freinage par temps sec, en raison d'une surface de friction de fait légèrement diminuée. Un autre inconvénient des disques perforés est leur relative fragilité.
Sur certains disques, ces « trous » ont des formes de petites encoches ou de demi-lunes, et jouent alors également le rôle de rainures.
Sécurité
Le frein à disque se prête bien à l'ajout d'un système anti-blocage des roues (ABS), permettant d'éviter le blocage des roues d'un véhicule en cas d'adhérence réduite. Le système fonctionne en relâchant brièvement la pression sur les freins lorsqu'il détecte une décélération anormale sur une ou plusieurs roues.
Galerie
- Différents types de disques
- Disque de frein arrière d'un camion. Sur les poids-lourds, ces éléments sont actionnés par un système pneumatique.
- Les motos Buell emploient des freins périmétriques : le disque est fixé à la jante et l'étrier (à triple piston) est à l'intérieur.
- Système de freinage monté sur le bogie d'un autorail japonais de la série 1000, desservant la ville de Kaizuka.
- Paire de roues d'un wagon central "Meridian" avec trois disques de frein, intégrée dans un bogie Görlitz VIII
- Vue du frein à disque avant droit d'une Porsche Boxster 986 phase 2 (frein à disque perforé).
- Étrier de frein à disque démonté, sur une Subaru Legacy. On distingue aisément les deux pistons de cet étrier flottant.
- frein amélioré (283 mm) sur Peugeot 106
- Vue d'un frein à disque ventilé de 370 mm, étriers 4-pistons d'une McLaren MP4-12C.
Notes et références
- https://www.hemmings.com/stories/article/the-first-car-with-disc-brakes-really-was
- "The Editor's Correspondence - Vintage Disc Brakes". Motor Cycling. London: Temple Press Ltd: 669. 26 September 1957.
- D.P. Morgan, "All About the RDC", Trains & Travel magazine, March 1953
- http://daimler-fighting-vehicles.co.uk/DFV-File%20Part%20Af%20-%20DAC%20Design%20&%20Development.pdf
- https://patents.google.com/patent/US2323052
- http://www.lexikon-der-wehrmacht.de/Waffen/Ar96.htm
- http://www.alanhamby.com/transmission.shtml
- Langworth, Richard M. (1994). Chrysler and Imperial: The Postwar Years. Motorbooks International. (ISBN 0-87938-034-9).
- Stéphane Schlesinger, Les inventions qui ont fait l'automobile, motorlegend.com du 27 mars 2018 , consulté le
- (en) Richard Lentinello, « The first car with disc brakes really was... », Hemmings.com, (consulté le ).
- « Mercedes-Benz - 626 ch pour le SLR ! », Challenges, .
- « Les différents types de disques de frein », Fiches-auto.fr, (consulté le ).
- Olivier Pernot, « Les freins carbone, céramique et DMC », Moto Revue, (consulté le ).
- « Avec l'amiante, ne pariez pas. Protégez-vous ! », INRS (consulté le ).
- (en) « The first brake assist system (BAS) was developed by Mercedes-Benz and introduced in 1996. » [PDF], nhtsa.dot.gov (consulté le ).
Annexes
Articles connexes
- Portail de l’automobile
- Portail de la moto
- Portail des camions
- Portail du génie mécanique
- Portail des technologies
- Portail du sport automobile
- Portail des sports motocyclistes