Composant monté en surface
Le composant monté en surface (CMS, SMD (surface mounted device) en anglais) désigne une technique de fabrication des cartes électroniques et, par extension un type de composants utilisés par l'industrie électronique. Cette technique consiste à braser les composants d'une carte à sa surface, plutôt que d'en faire passer les broches au travers.
Pour les articles homonymes, voir CMS.
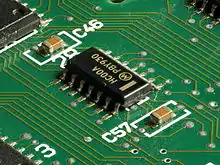
Historique
La technique des « Composants Montés en Surface » (CMS) a été développée dans les années 1960 et a commencé à être largement diffusée dans les années 1980. La plupart des premières recherches dans ce domaine ont été effectuées par IBM[réf. nécessaire].
Les composants ont été repensés mécaniquement pour posséder de petites terminaisons métalliques ou de petites broches à leurs extrémités pour pouvoir être brasés directement à la surface des circuits imprimés.
Ils ont ainsi vu leur taille diminuer progressivement (on trouve aujourd'hui couramment des résistances qui mesurent 0,06 × 0,03 pouces : taille 0603 équivaut à 1,6 × 0,8 mm, et des formats plus petits existent : 0402, 0201, 01005.).
Au fil du temps, les CMS sont devenus plus communs que les composants traditionnels, permettant un plus fort taux d'intégration des cartes électroniques.
Ils sont ainsi bien adaptés à un degré élevé d'automatisation dans la fabrication, réduisant les coûts de production et augmentant la productivité. Les CMS sont jusqu'à dix fois plus petits que leurs équivalents traditionnels, et leur coût peut être inférieur de 25 à 50 %.
Avantages et inconvénients
Les composants électroniques des générations précédentes (dits traditionnels ou traversants) étaient d'assez grosse taille et équipés de broches destinées à traverser le circuit imprimé, la soudure se faisant du côté opposé de la carte afin de relier électriquement les broches au circuit imprimé.
La miniaturisation constante des cartes électroniques a rendu ce système quasi obsolète :
- Les composants sont plus petits et plus légers ;
- Les circuits imprimés n'ont plus à être percés ;
- L'assemblage peut être automatisé facilement ;
- Les tensions de surface centrent les composants automatiquement sur leur plage[réf. nécessaire] lors de l'étape de brasage. Les marges de placement sont ainsi augmentées ;
- Des composants peuvent être placés plus facilement sur les deux faces de la carte, ce qui augmente la densité de composants mais aussi la complexité du circuit imprimé ;
- Les résistances et inductances électriques parasites sont diminuées, augmentant ainsi les performances en hautes fréquences ;
- Les propriétés mécaniques en vibration sont meilleures ;
- Le coût global est diminué.
Les seuls inconvénients se situent au niveau du contrôle et de la maintenance, posant des problèmes supplémentaires aux techniciens assurant le contrôle des fabrications (utilisation de machines d'inspection par rayons X) et le dépannage, particulièrement lorsqu'ils doivent changer un composant.
- Différents types de composant montés en surface
- Condensateurs à côté d'un trombone.
Méthodes de brasage
Brasage par refusion
La refusion (en) est utilisée pour les cartes contenant soit uniquement des CMS, soit des CMS dont le brasage ne peut se faire que par cette technique (BGA). La pose de CMS sur une carte est rapide, simple et fiable par rapport aux composants traversants. Le circuit imprimé nu est d'abord sérigraphié : les plages du circuit imprimé sont recouvertes d'une pâte à braser grâce à un pochoir métallique (clinquant) : seuls les emplacements des terminaisons des composants sont recouverts. Puis les composants sont posés sur le circuit par les machines de placement. Finalement la carte passe dans un four (en), où la chaleur fait refondre la pâte déposée pour former la brasure sans risque de surchauffe des composants électroniques.
Les cartes électroniques actuelles sont très souvent équipées de composants sur leurs deux faces. Elles nécessitent donc deux passages sur la ligne de production : un pour chaque face. Ce sont les tensions de surface entre les plages et les pattes des composants, ainsi qu'un éventuel point de colle sous les composants, qui font que ceux-ci ne tombent pas lors de la deuxième refusion.
Brasage à la vague
Cette méthode est utilisée en cas de mixité des CMS et composants traditionnels. Elle consiste à déposer un point de colle aux futurs emplacements des composants au lieu de sérigraphier les plages. Les composants sont ensuite posés de la même manière que précédemment avant de polymériser la colle au four ou en étuve. Cela permet de placer ensuite des composants traditionnels (traversant le circuit imprimé) de l'autre côté de la carte.
La soudure se fait ensuite grâce à une vague d'étain en fusion, la carte passant au-dessus : au contact de l'étain et par capillarité les terminaisons des CMS et les broches des composants traversants sont soudées sur le circuit.
C'est ainsi une manière de mixer les deux technologies, l'intérêt est double :
- Tous les composants n'existent pas en version CMS ;
- Certains doivent avoir une résistance mécanique supérieure à ce que la technologie CMS peut apporter (cas de certains connecteurs pour des questions de résistance à l'arrachement par exemple).
Directive européenne 2002/95/CE - RoHS
La transition vers l'application de la directive européenne 2002/95/CE - RoHS - bannissement du Plomb, Chrome hexavalent, Mercure, Cadmium, PBB et PBDE.
Sans parler de la miniaturisation et de l'intégration de fonctions électroniques de plus en plus puissantes dans les composants, l'évolution majeure en cours est le passage de l'industrie électronique au « sans plomb ».
En effet, jusqu'à il y a peu, les brasures étaient réalisées à base d'étain-plomb (SnPb). Mais une directive européenne vient bannir le Plomb, Chrome hexavalent, Mercure, Cadmium, PBB et PBDE à partir de 2006 (directive RoHS) no 2002/95/CE.
L'avantage du plomb était notamment d'abaisser le point de refusion des alliages d'étain. Les nouveaux alliages sont couramment à base d'étain, argent et cuivre (SnAgCu) : la température de refusion a augmenté de plusieurs dizaines de degrés (on dépasse aujourd'hui les 260 °C).
Cette augmentation de température a plusieurs conséquences :
- Des problèmes d'ordre technique pour les fabricants de composants, ceux-ci devant pouvoir supporter des températures plus élevées et des chocs thermiques plus importants ;
- L'obligation de gérer de manière plus stricte qu'auparavant les « Niveaux de Sensibilité à l’Humidité » (en anglais Moisture Sensible Level : MSL). En effet, une reprise d'humidité des composants avant l'étape de refusion peut conduire à leur destruction[pourquoi ?]. Emballage sous vide, stockage dans des armoires sèches, régulation du taux d'humidité des ateliers sont autant de nouvelles contraintes à intégrer pour les entreprises ;
- Trouver un moyen de supprimer les « whiskers » (pousse de fibres cristallines de quelques micromètres capable de créer des courts-circuits), ces derniers sont absents lors du mélange avec le plomb ;
- Une gestion compliquée à mettre en œuvre pour la phase de transition et donc la mixité des composants prévus pour le « sans plomb » et les autres ;
- Les problèmes d'obsolescence de composants en fin de vie qui ne seront pas adaptés au « sans plomb » faute de débouchés commerciaux ;
- Des investissements nouveaux sont à réaliser pour adapter les équipements de production à ces nouvelles contraintes ;
- Des consommations d'énergie plus importantes (de 10 à 20 %), compte tenu de l'augmentation des températures de refusion ;
- Une requalification systématique des processus de fabrication s'avère également nécessaire.
Notes et références
Voir aussi
Articles connexes
Liens externes
- Remplacement du plomb dans les alliages de soudure en microélectronique, whiskers
- Réalisation d'un four à refusion avec un mini-four
- Optimisation temps de setup machine SMD Pick&Place
- (en) Article décrivant la norme JEDEC-J-STD-033 concernant les niveaux de sensibilité à l'humidité des composants électroniques
- (en)+[PDF] Intersil - Guidelines for Soldering Surface Mount Components to PC Boards
- Portail de l’électricité et de l’électronique